The Basics and Capabilities of Our Rubber Extrusions
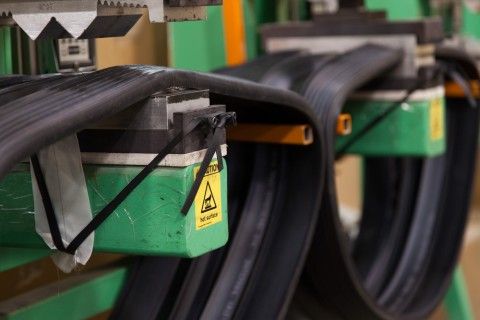
At Elbex, our rubber extrusions are created by forcing uncured rubber compounds through a die to achieve the desired shape, and then curing it in a high-temperature salt bath. This process is ideally suited for high-volume runs, allowing us to produce more material in a shorter time period. Of course, there is more to our rubber extrusions than this. Here is a closer look at what we can do for you.
Key Capabilities
Elbex can produce extrusions, cords, tubing, sheeting, and gaskets to a wide range of specifications. This includes manufacturing products that meet ASTM, AMS, SAE, RMA, and military specifications. We work with a wide range of materials with custom in-house batch material mixing. EPDM, nitrile, PVC, silicone, neoprene, and urethane are just a few of the materials we can use based on the needs of your project. Better yet, most of our elastomers are available in both sponge and dense profiles.
In-house tooling, design, and production enables our team to produce custom products and even assist with rubber compound design. High-speed cutting, punching, printing, splicing, taping, and secondary vulcanization adds even more value to our services. Of course, all work has complete quality control from design to the finished product.
Batch Sizes
Because of our strong focus on custom design, there are minimum order requirements for each project. These requirements vary based on material and profile size and are designed to utilize at least one full batch of rubber material. For example, a material batch of silicone will be 100 pounds, while it may be 500 to 600 pounds for materials like EPDM.
Do you need rubber extrusions for your next project? Whether you need custom or standard extrusions, the experienced team at Elbex has the capabilities to make it happen. Contact us today to get started on your project.
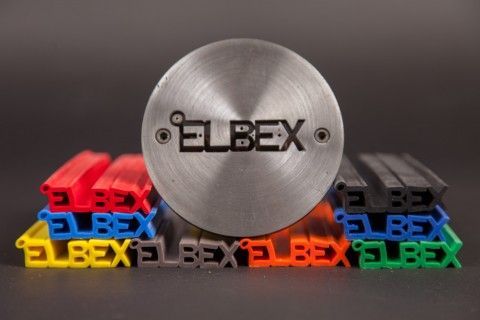
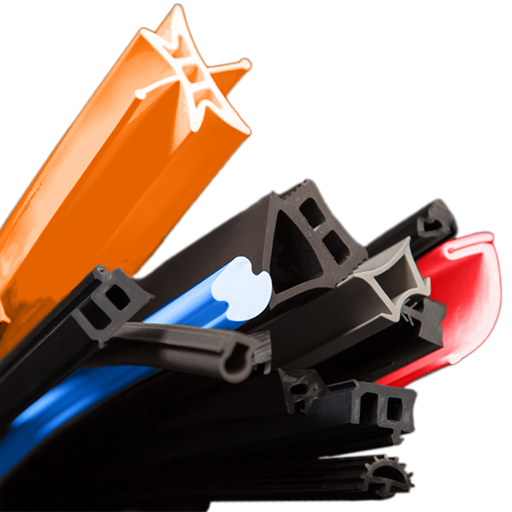
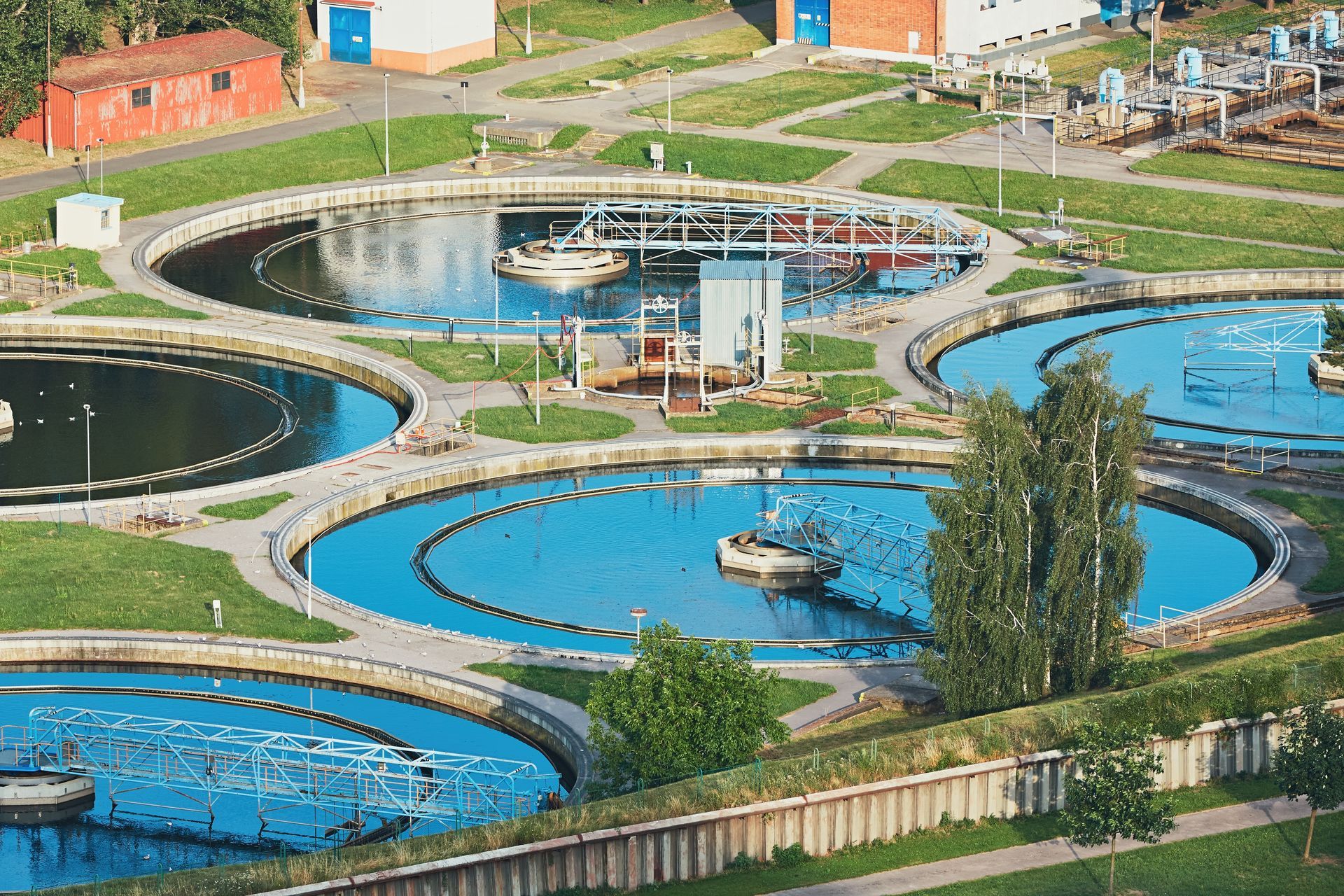