Rubber Extrusion Manufacturing
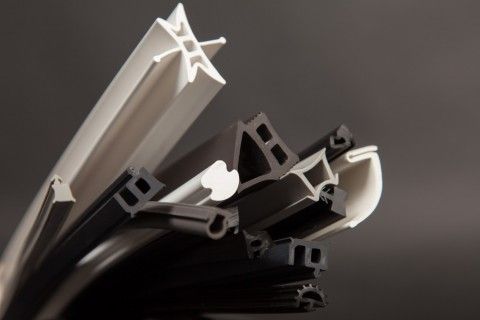
Manufacturing rubber extrusions is a process which has been around for more than a century. Over that timeframe, many advancements have been made in the extrusions industry.
Manufacturing Rubber Extrusions
Rubber is a naturally occurring elastomer. But today, synthesized rubber compounds outproduce natural gum rubber products.
Today, a rubber extrusion manufacturer — after completing the design phase and having selected the elastomeric material — will create a die to make the desired shape and size of an extrusion.
The rubber material is fed into a hopper (typically suspended above a conveyor). Here the rubber is gravity fed onto the conveyor which in turn moves the rubber towards the die utilizing a rotating screw. Once the rubber softens, it moves through the die, swells, and takes the shape of the die.
Additional steps can be taken to ensure the finished extrusion is customized for its application.
Other Forms of Rubber Extrusions
There are other processes which allow manufacturers to create other types of extrusions. Usually these variations are used depending on the rubber that is being extruded.
For example, injection molding requires the rubber to be heated and injected into a mold cavity. This is a popular alternative to the standard rubber extrusion process.
Plastic extrusion is another alternative where the raw material takes the shape of nuggets or kernels before it passes through a die. Co-extrusion is a process where two separate extruders are connected to a single die. This allows for mixing different batches of rubber.
When you are selecting a rubber extrusions manufacturer, make sure you select a company which has experience with extrusions, has the ability to create customized solutions, is ISO-certified, and solve complex problems.
Contact ELBEX
today for your next rubber extrusion products.
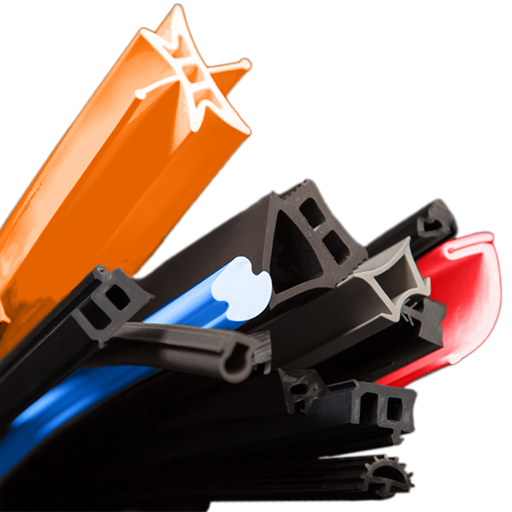
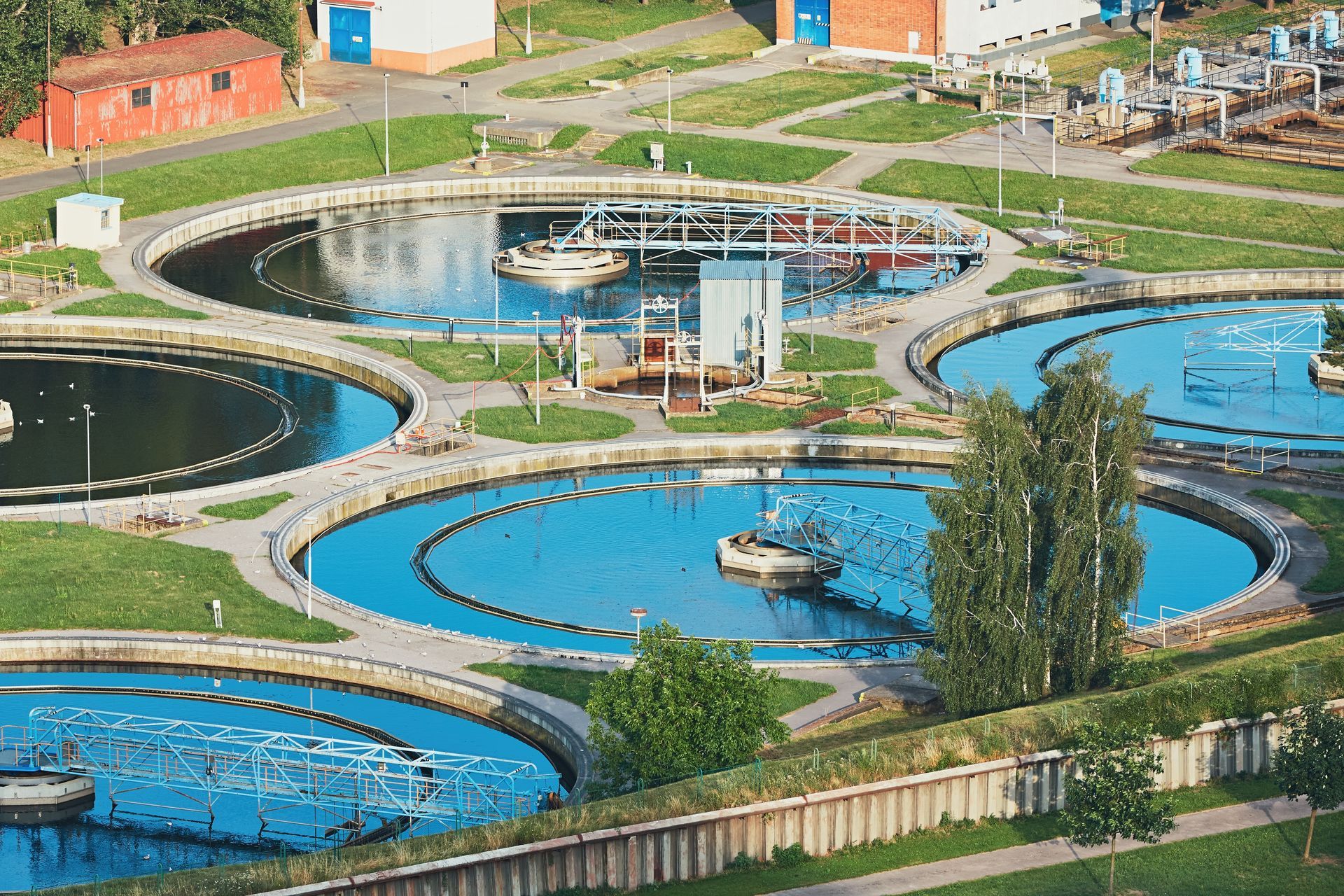
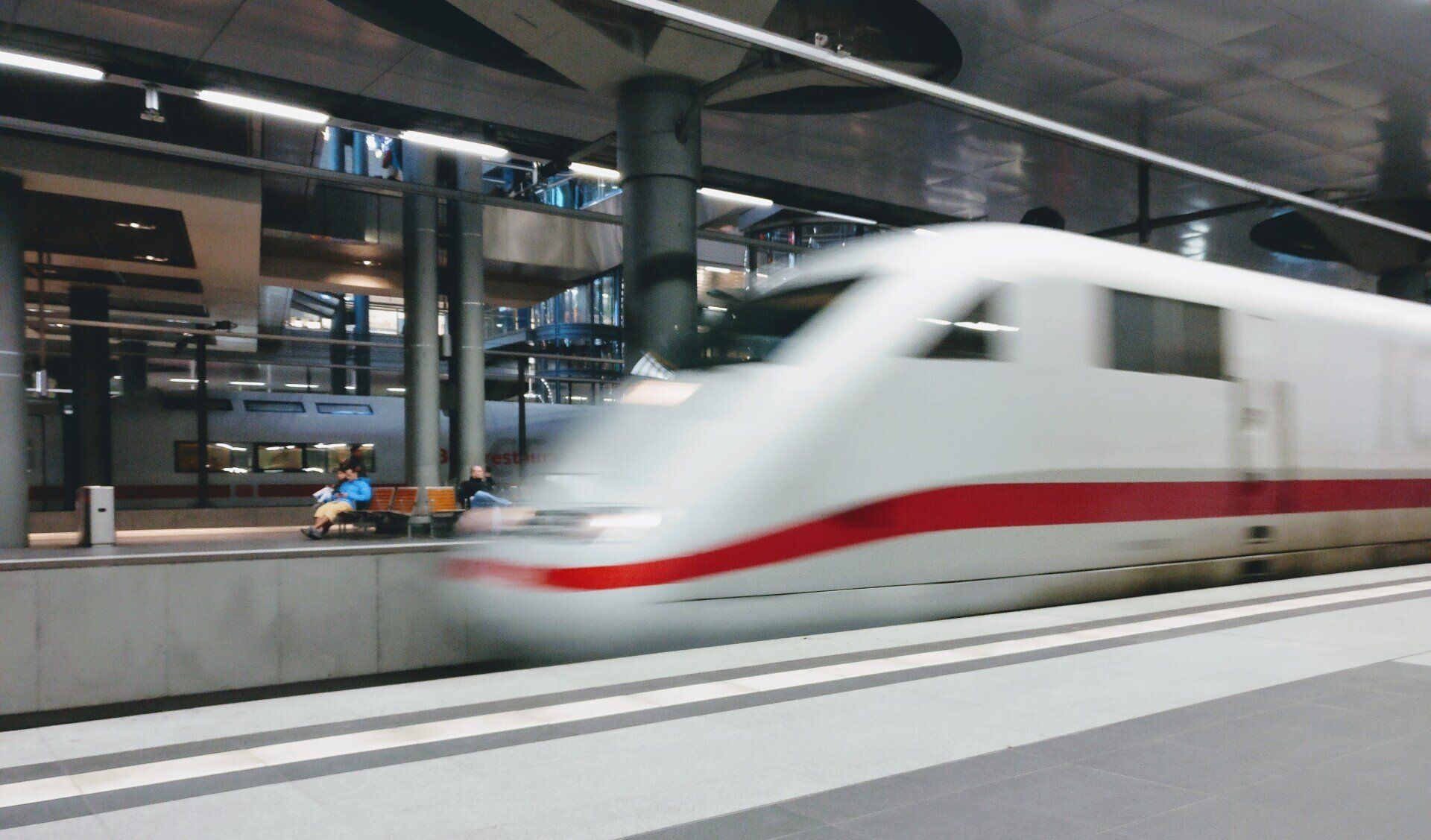