Everything You Need to Know About Expansion Joints
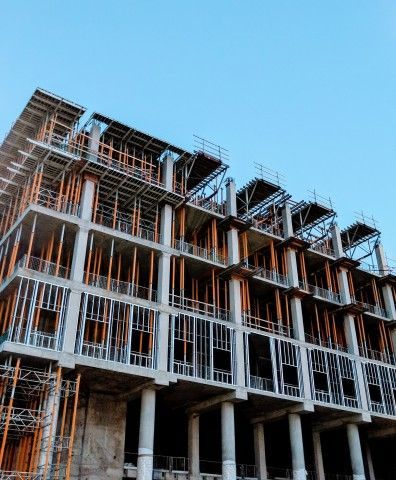
Expansion joints play a vital role in a wide range of construction projects, helping to hold separate components together while also lessening the impact of vibrations and temperature-related expansion and contraction. Quality materials and design are an absolute must for this important rubber extrusion.
Protecting Structural Applications
Expansion joints protect building materials from structural stress, which is primarily caused by temperature-related activity. Concrete, building faces, glass, and even pipelines expand and contract as a result of seasonal warming and cooling, as well as exposure to other nearby sources of heat. Without an expansion joint in place, the added pressure can cause materials to crack. Expansion joints help make the application more “flexible” by absorbing this stress and keeping materials from rubbing against each other. Expansion joints can also minimize damage from natural ground settling.
The Use of High-Quality Materials
Unsurprisingly, the quality of a rubber expansion joint is directly tied to the quality of the materials used in manufacturing. At Elbex, we use natural rubber products from high-quality sources to ensure that they will meet the desired performance requirements of a particular application. Accounting for unique environmental hazards (such as extreme temperatures or chemical exposure) helps enhance the longevity of a custom expansion joint.
For reliable expansion joints for your next project, contact Elbex. Our experienced team uses a wealth of industry knowledge to ensure that your custom-designed extrusions are the right match for your application.
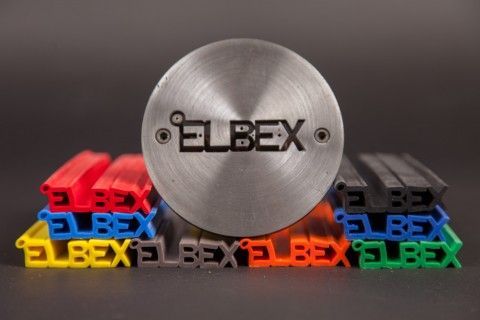
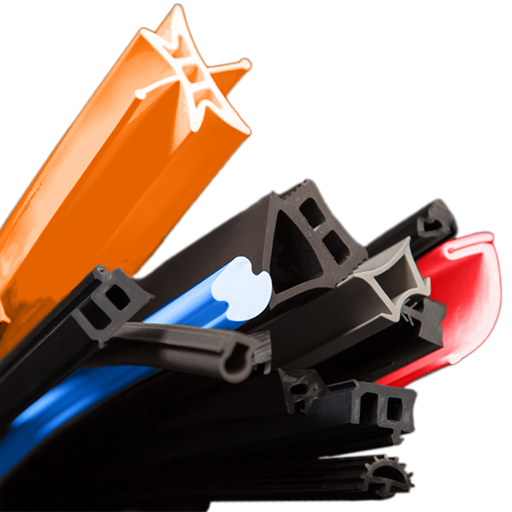