Exploring the General Properties of Elastomers
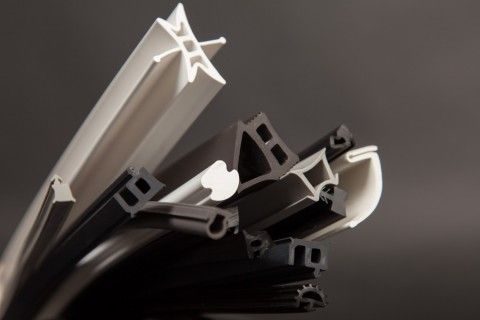
ELBEX rubber and silicone extrusions are used in a wide range of industries, and for countless applications. This is made possible through the many types of elastomers we use, which allow us to optimize our extrusions for unique performance requirements.
Physical Properties of Elastomers
Elastomers are mixed with many different chemicals and compounds to achieve the desired physical properties in an extruded product. Basic polymers can also be used to create compounds with unique properties.
Silicone Rubber, EPDM and Neoprene
Silicone rubber, EPDM, and Neoprene are among the most common elastomers we use. Silicone rubber is a semi-organic synthetic that is made with sand and an alkyl or aryl halide. Though it looks and feels like natural rubber, it has a different chemical structure that gives it a flexible, but weak chain. Though it can withstand a range of temperatures and offers good fatigue and flex resistance, it has poor tensile, tear, and abrasion resistance. On the other hand, elastomers like Neoprene offer good resilience, abrasion strength, and weather resistance.
Wide Range of Elastomers
The wide variety of elastomers means that some will be resistant to the same chemicals that are a vulnerability for others. One elastomer could be resistant to animal and vegetable fats, chemicals, and acids, while another would be attacked by those same things.
For example, silicone rubber is resistant to many oxidizing chemicals, as well as ozone and UV light. However, it is vulnerable to many solvents, oils, and acids — and even steam. Understanding the properties of each material is vital for achieving a successful, durable extrusion for a desired application.
By working with a wide range of elastomers and understanding their unique properties and capabilities, the ELBEX team is well-equipped to produce extrusions that meet the needs of your application. Contact us today to learn how we can help with your next project.
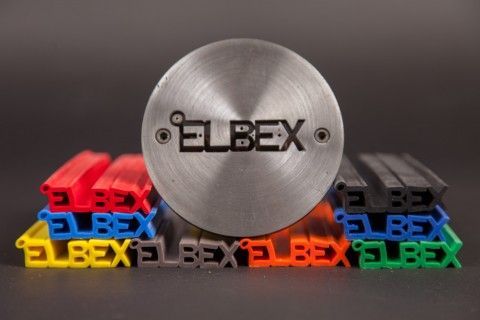
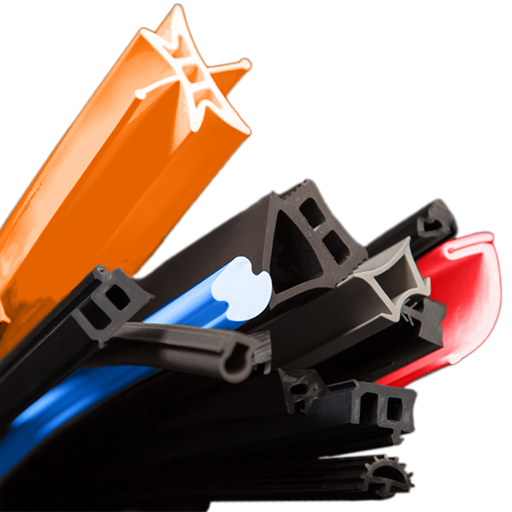